2013 KCSE Metalwork Past Paper
4.3.1 Metalwork Paper 1 (445/1)
SECTION A (40 marks)
Answer all the questions in this section in the spaces provided.
1. a) Define the term “apprentice” as applied in the engineering field.
b) Explain the term “break-even” as used in business.
2 a) List three uses of a steel rule.
b) (i) With the aid of sketches, distinguish between a dot punch and centre punch.
(ii) State two uses of a dot punch.
3 a) State two reasons for edge treatment on sheet metal articles. b) Outline the procedure of finishing a work piece by painting.
4 a) Outline the process of case hardening a vee block.
b) State two effects of each of the following alloying elements on iron:
(i) chromium;
(ii) manganese.
5 a) Define the term “upsetting” as used in forging.
b) State two reasons for twisting metal bars.
6 a) With respect to needle files, state:
(i) their use;
(ii) the reason for not fitting a handle;
(iii) the reason for knurling one end.
(b) Figure 1 shows two mild steel plates of equal thickness to be rivetted.
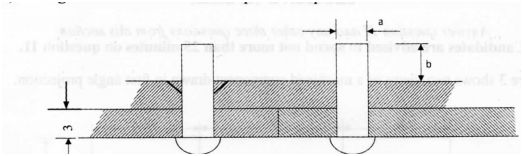
Determine:
(i) rivet diameter marked a;
(ii) heading allowance marked b. (3 marks)
7 (a) State the:
(i) effect of prolonged heating in brazing; (1 mark)
(ii) reason for concentrating heat on the thicker piece of metal when brazing two metals. (1 mark)
(b) With reference to arc welding:
(i) define the term “tack welding”;
(ii) state the use of tacks.
8 With the aid of labelled sketches, distinguish between parallel tuming and facing in lathe work. (3 marks)
9 State four possible causes of bums in a workshop. (2 marks)
10 Figure 2 shows an isometric drawing of a block. Sketch in third angle projection, the orthographic views of the block. (6 marks)
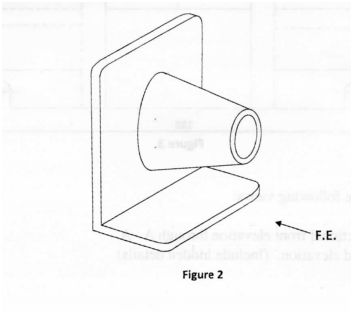
SECTION B (60 marks)
Candidates are advised to spend not more than 25 minutes on question 11.
11. Figure 3 shows two views of a machined component drawn in first angle projection.
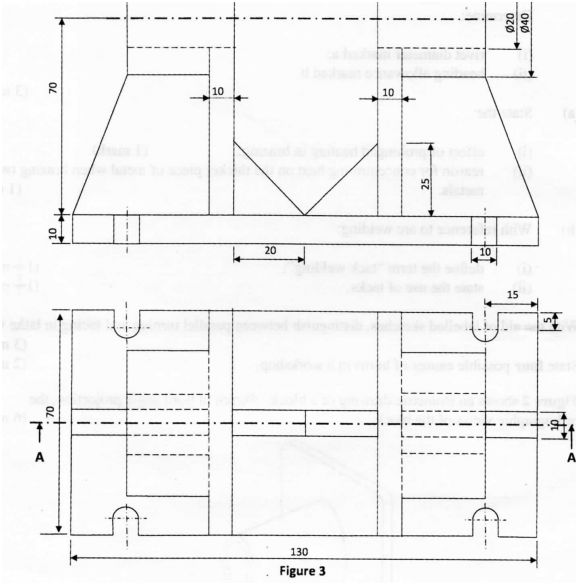
Draw full size, the following views:
(i) sectional front elevation through A – A.
(ii) end elevation. (Include hidden details). (15 marks)
12. a) State four safety precautions to be observed before switching on power supply of an electric arc welding equipment. (4 marks)
b) With respect to arc welding:
(i) state the two methods of striking the arc; (1 mark)
(ii) give one advantage and one disadvantage of using each method. (4 marks)
c) Name and illustrate four welding defects. (6 marks)
13 a) With the aid of sketches, explain the procedure of drilling a hole on a centre lathe machine. (10 marks)
b) State and sketch two methods of producing a short taper on a lathe machine. (5 marks)
14 a) Outline the procedure of cutting intemal threads on a round bar using a die stock. (5 marks)
b) Name and sketch the three thread taps which make a set.
c) Sketch in pictorial a hand file and label all its parts.
15 a) State two causes for each of the following problems in drilling:
(i) worn out comers of cutting edges on a twist drill; (2 marks)
(ii) chipped cutting lips; (2 marks)
(iii) rough walls of a drilled hole. (2 marks)
b) With the aid of labelled sketches show how:
(i) a centre punch is ground on a grinding wheel.
(ii) the grinding lines should appear on the ground surface of the centre punch.
c) State three safety precautions to be observed when grinding. (3 marks)
2013 KCSE Metalwork Past Paper-Marking Scheme/Answers
5.3.1 Metalwork Paper 1 (445/1)
1. (a) An apprentice is a person on the job training for a specified period. (1 mark)
(b) When no profit or loss is made in any sales/business. (1 mark)
2. (a)Uses of a steel rule:
measuring
marking
testing of flatness/straightness.
b)
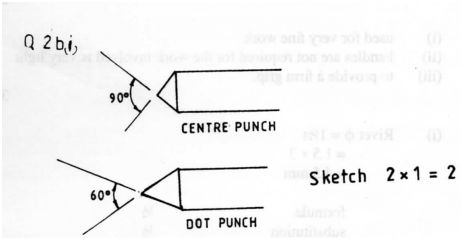
3. (a) -emphasis lines/markings
– locate centre of circles or arc
make edge safe
made edge strong
improve aesthetics
b)clean
apply premises coat
apply lst coat
apply finishing coat
4 a) – clean the metal
– heat to bright red
– cool it in caseinate compound
– re-heat
– quench
b) (i) Chromimium – imparts stainless properties and adds to hardness.
(ii) Manganese – increases resistance and adds strengths.
5. a) Process of increasing thickness at expense of length.
b) – To increase its strength.
– For decoration purpose.
6 a) (i) used for very fine work.
(ii) handles are not required for the work involved is very light
(iii) to provide a firm grip.
b) (i) Rivet
= 1.5 x 3
=4.5mm
(ii) Hea
= 1.5×4.5
= 6.75mm
7 a) (i) It causes scale to work into the joint.
(ii) So that both parts are brought to the correct heat at same time.
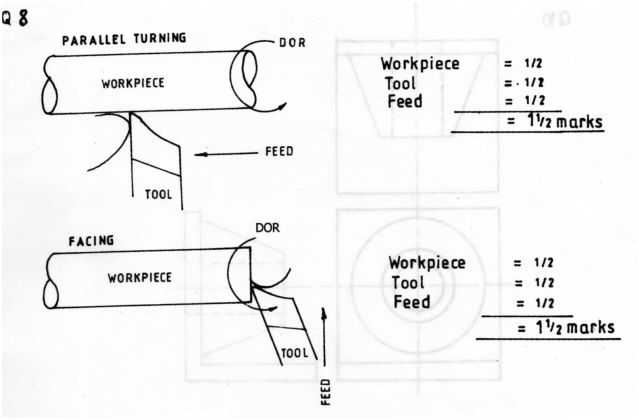
(b) (i) They are short runs at intervals along the joint.
(ii) They assist in keeping the plates to be welded in perfect alignment or Holding two pieces of metals together.
9. Dry heat
Electricity
Lightening
workpiece
Tool
Feed
Revolving wheels/belts/ropes
Acid
Steam
Hot metals/objects
Fires or flames
10.
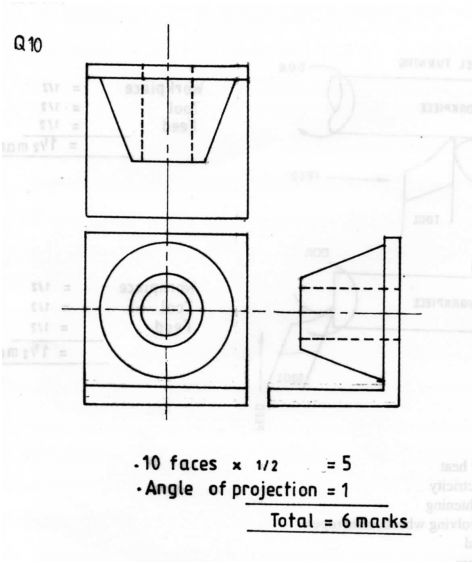
11.
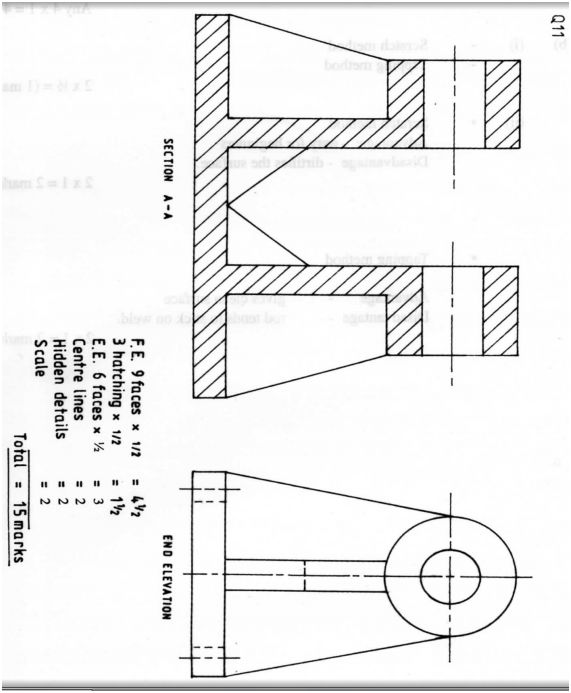
12. a) Verify that all cables insulations are intact.
Make sure all terminals are secure.
Ensure that the conductors used are of the correct current rating.
Ensure that the equipment is adequately earthed.
Be familiar with locations of the “off” positions of the mains switch.
b) (i) – Scratch method
– Tapping method
ii) ‘ Scratch method
Advantage: – easy for beginners
Disadvantage – dirtifies the surface.
Tapping method
Advantage – gives clean surface
Disadvantage – rod tends to stick on weld.
c)
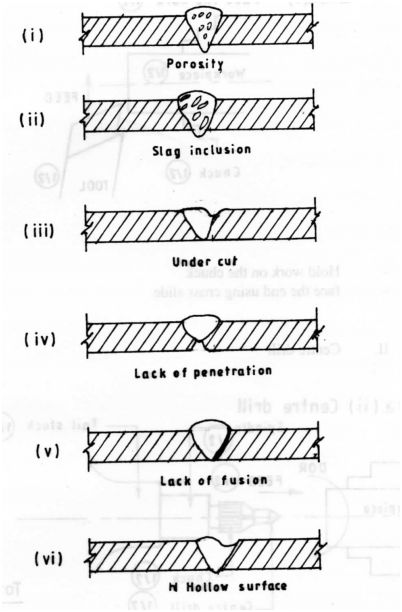
(iv) Luck ll penetration
(v) Lu! of fusion
13. a) (i)
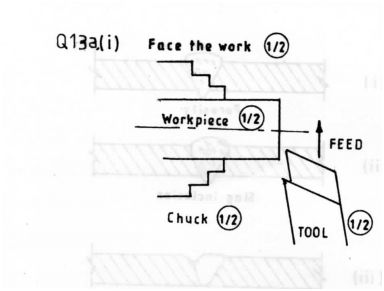
Hold work on the chuck
face the end using cross slide
Centre drill
Centre drill
(ii)
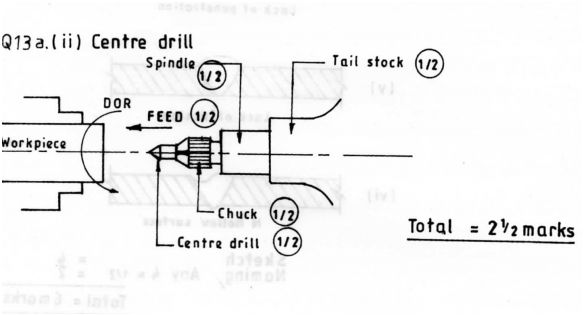
use drill chuck to chuck to hold the centre drill
hold chuck on the spindle of the tailstock.
lock the tailstock on the machine bed.
feed the centre drill into the rotating work-.
13 a)(iii)
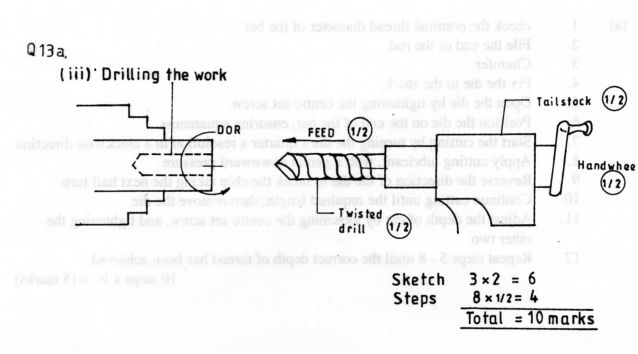
– Replace centre drill with twin drill.
– feed the drill into the rotating work using tailstock wheel
(b) Short taper tuming methods
c)
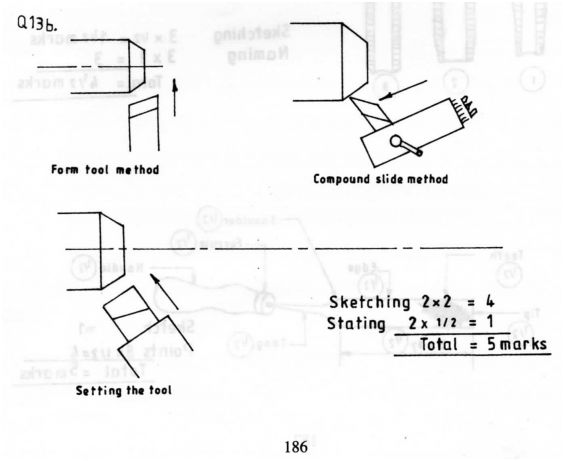
14. (a) . check the nominal thread diameter of the bar.
File the end of the rod.
. Chamfer.
Fix the die in the stock.
. Open the die by tightening the centre set screw.
Position the die on the end of the bar, ensuring squareness.
. Start the cutting by turning the die a quarter a resolution in a clockwise direction
. Apply cutting lubricant, with a gentle downward pressure
Reverse the direction of the die to break the chip taking the next half tum
Continue cutting until the required length, then remove the die
Adjust the depth of cut by loosening the centre set screw, and tightening the other two Repeat steps 5 – 8 until the correct depth of thread has been achieved.
10 steps x 56 = (5 marks)
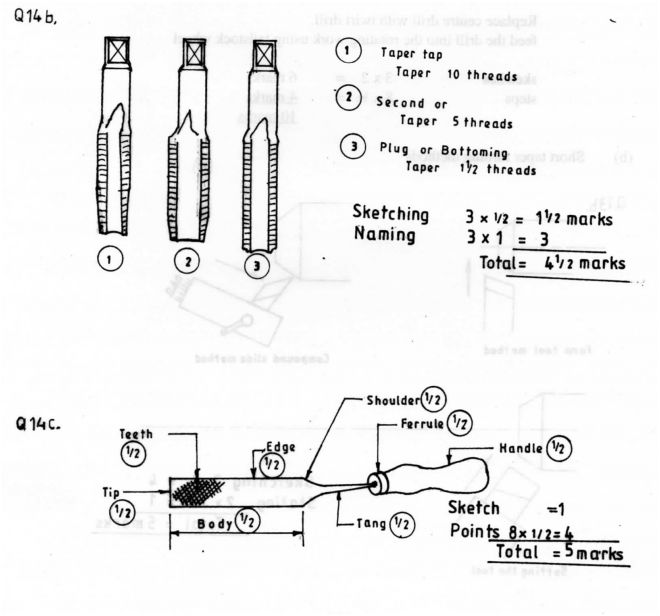
l5. (a) (i) Excessive speed for the material being cut.
Lack of a suitable cutting solution.
(ii) Excessive lip clearance angles.
Too heavy a feed.
(iii) Drill is blunt
No cutting solution
Too much feed
Drill is badly ground.
15.
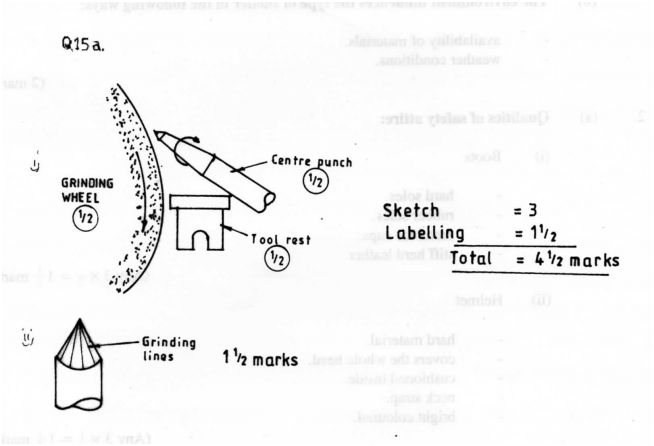
Safety precautions when grinding.
(i) Use the whole face of the wheel to maintain its flatness
(ii) Goggles should be wom all the time.
(iii) The tool rest must beadjusted to be close enough to the wheel.
(iv) Work should be firmly held.
(v) Use the guards on the grinding machine.
(vi) Never touch the revolving wheel while grinding.